Peritoneal Dialysis Solution (CAPD) Production Line
Peritoneal Dialysis Solution (CAPD) Production Line Introduction:
Our Peritoneal Dialysis Solution production line, with Compact structure, occupying small space. And Various data can be adjusted and save for welding, printing, filling, CIP & SIP like temperature, time, pressure, also can be printed out as required. The main drive combined by servo motor with synchronous belt, accurate position. Advanced mass flow meter gives precise filling, volume can be adjusted easily by man-machine interface.
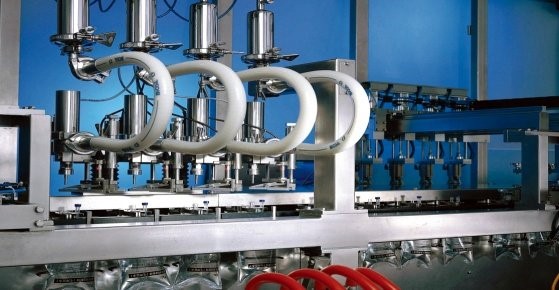
Application
For CAPD solution bag printing, forming, filling and sealing, tube welding, PVC bag making machine.

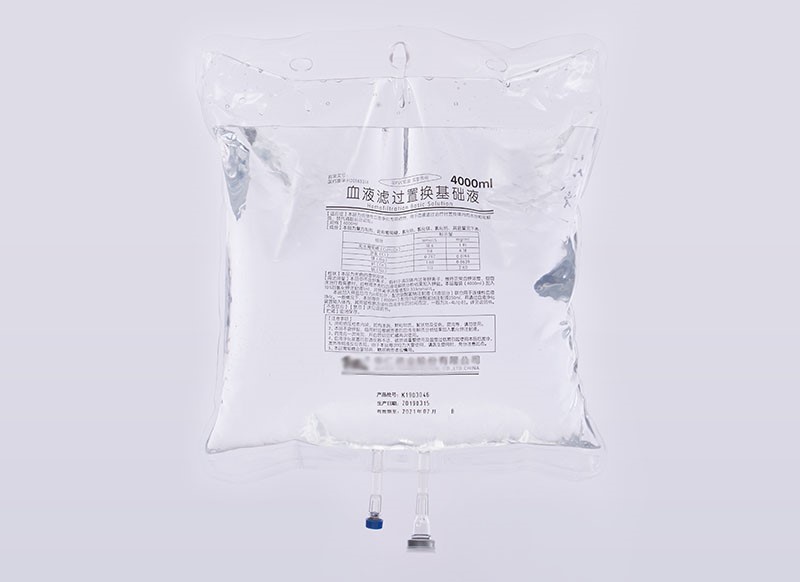
CAPD Dialysis production line Production Procedures
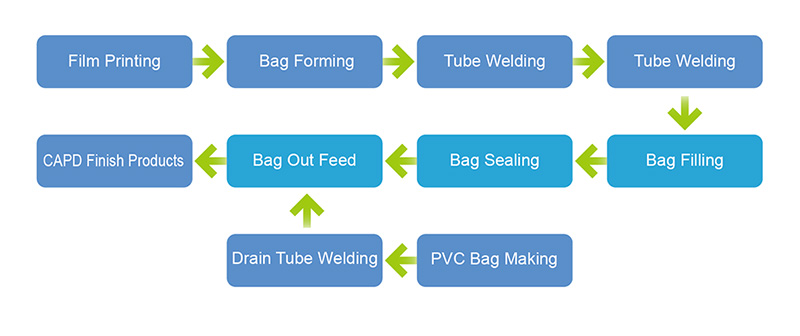
Bag Forming Station
- Peripheral welding with double open mold structure and fluctuation mold is equipped with cooling plate, make fluctuation mold the same temperature, and ensure that equipment in the molding process and stop will not baking hot membrane material; Improved the product quality.
- Heating pipe and thermocouple in aluminum alloy heating plate, heating and heat transfer are uniform, temperature control is precision, reduced the heat loss, won't appear the actual temperature and display temperature not consistent, so as to ensure welding qualify rate.
- 100% utilization of the film, no waste edge between bags and groups.
- The forming mold is specially designed. The last formed bag of the former group will be cut together with the first formed bag of the latter group. It is good for the dragging of film when stretching bags. Only one system can guarantee the stretch of film and stretch of bag can be done synchronously. (guaranteed the same tension film length of each time between every group, namely there is no waste edge between different groups - the domestic manufacturer exist waste edge between each group.)
- When changing mold for different specifications of products, only need to change upper mold, the bottom mold is adjustable general mold, which can greatly save replacement debugging time. Forming mold is made by special materials and special process of special mold manufacturers, ensured not mark for the quality and service life of 100 million bags.
Bag Cold Joint Welding & Waste Edge Removing Station
- As per the characteristics of welding plastic, cold welding should be adopted immediately to form it after two high-temperature welding. This can both ensure the plastic welding firmness and bring the good appearance. Therefore, the 2nd welding ports need cold welding, with welding temperature of actual cooling water temperature (15ºC-25ºC), the time and pressure is adjustable.
- With patent design, the waste edge removing station is simple and reliable, high pass rate up to 99% and above. The upper and lower guide rods clamps the waste film after bag forming and tear it up by guide cylinder, to complete the bag forming. The triangular waste edge is collected by special device. The automatic waste edge removing station can not only reduce the negative effects of artificial tearing, but also ensure the nice bag shape.
Filling station
- Adopt the E + H mass flowmeter measurement and high pressure filling system.
- A frequency control pump controls the pressure, use the high-pressure resistant medical silicone pipe to connect the pipeline, easy maintenance, no cleaning dead spot.
- High filling accuracy, no bag and no qualified bag, no filling.
- Filling heads adopt patent technology of smooth surface sealing, no contact with ports interwall so no friction to generate the particles; it also avoids the overflow of solution which caused by change of ports size to make the ports unsealed with the filling heads.
Electric Control Cabinet
- It adopts advanced PLC control and integrated valve terminal method, simple circuit, fast operation reaction, safe and reliable running. Filling part is integrated with sealing part into one unit, it only needs one electric control system and one man machine interface operation unit; at least one operator is reduced, avoids the disadvantages like incompatibility between two operators, and increases the safety and reliability of the equipment.
- Touch screen display and operates all temperature control accurately. Especially gives small fluctuations in starting and stopping moments, tolerance can be ±1℃.
- Printing panel is installed on the aluminum plate by S/S stud bolt, avoid the hole thread loose on the plate after long-term use.
- The film roll is positioned by uniform tension from 4 sides to ensure the film tension and smooth running. The film roll left and right sides are fixed by the adjustable positioning plate, to ensure the feeding speed and accuracy.
- Preheating station and heat sealing station adopt spring-loaded needle probe to detect the mold temperature, convenient installation and disassembly, uneasy to broke, tolerance within ± 0.5℃.
- Change the way of sealing positioning to protect the cylinder, avoid long-term heating on it.
- Professional external wiring, separate the wire following different classifications, good appearance and convenient maintenance.
- Fix the lower mold, but retain the cooling plate, to protect the film when the machine shuts down.
- Surrounding heat sealing adopts special mold, install the cooling plate of upper mold with spring-loaded.
- Add the automatic feeding system to resolve the problem of blocking and jamming, reduce the labor intensity. Add the ionic wind cleaning and recovery device to enhance the product clarity.
Send your message to us:
Write your message here and send it to us